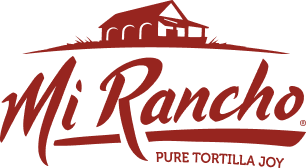
Menu
Cart
Careers
Join our team and be a part of our storyAt Mi Rancho, all employees are considered part of the family and are an integral part of the company’s success. We operate with a simple principle from our patriarach- you give respect, you get respect back. Pure Tortilla Joy doesn’t just describe our delicious tortillas. It refers to the joy every employee feels coming to work at Mi Rancho each day. All positions are based at our Elk Grove, CA headquarters.
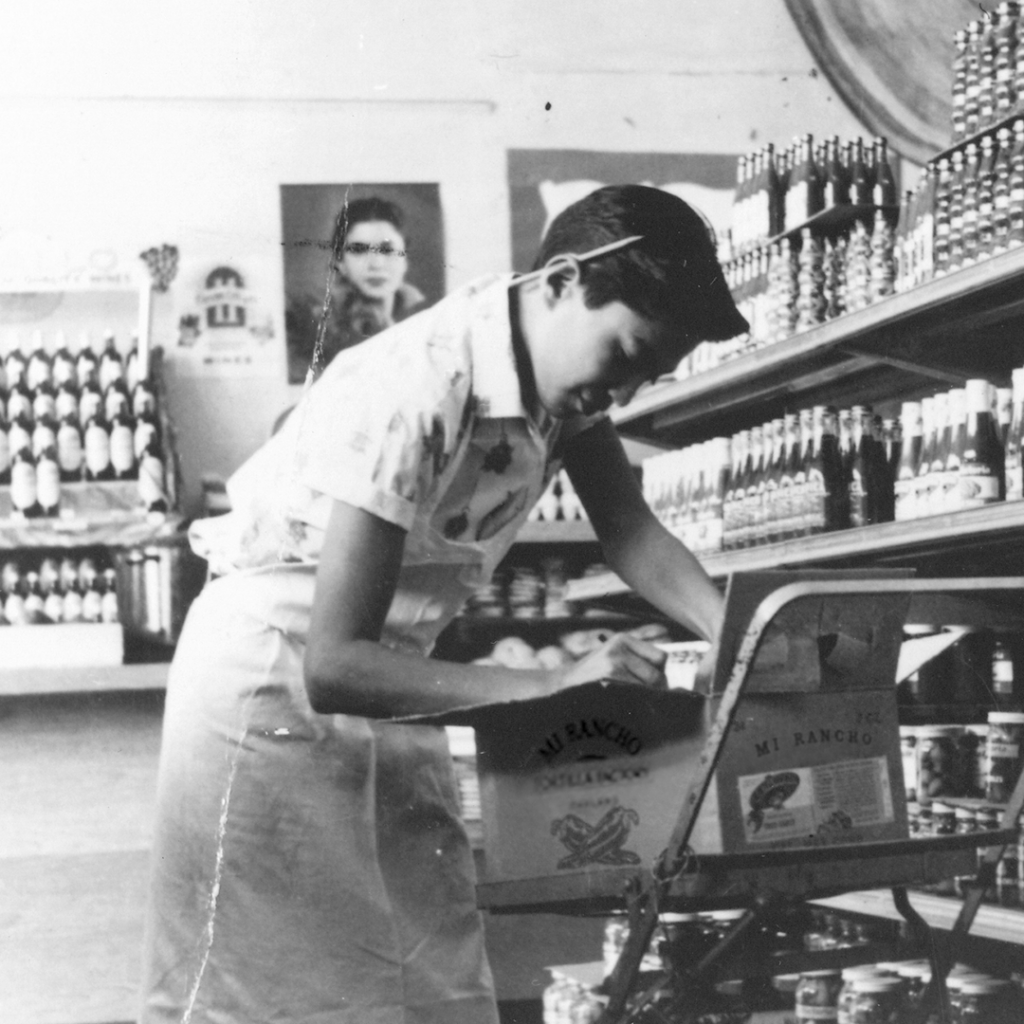
For us, it's never been about just making tortillas.
Our story began on 7th Street in Oakland over 80 years ago, and we remain committed to this pursuit — to share our heritage and passion with each of you through authentically crafted foods.
